As an employer, you have the responsibility to ensure that your employees have a safe and healthy environment to work in. Whether all of your employees are on-site, you have remote workers, or you offer your services at client sites, you need to provide the necessary tools and information so that your team do not suffer accidents and injuries. Workplace accidents can cost businesses billions every single year, but if you keep up to date and have the knowledge and follow the right processes and procedures, you can limit your exposure to this business risk.
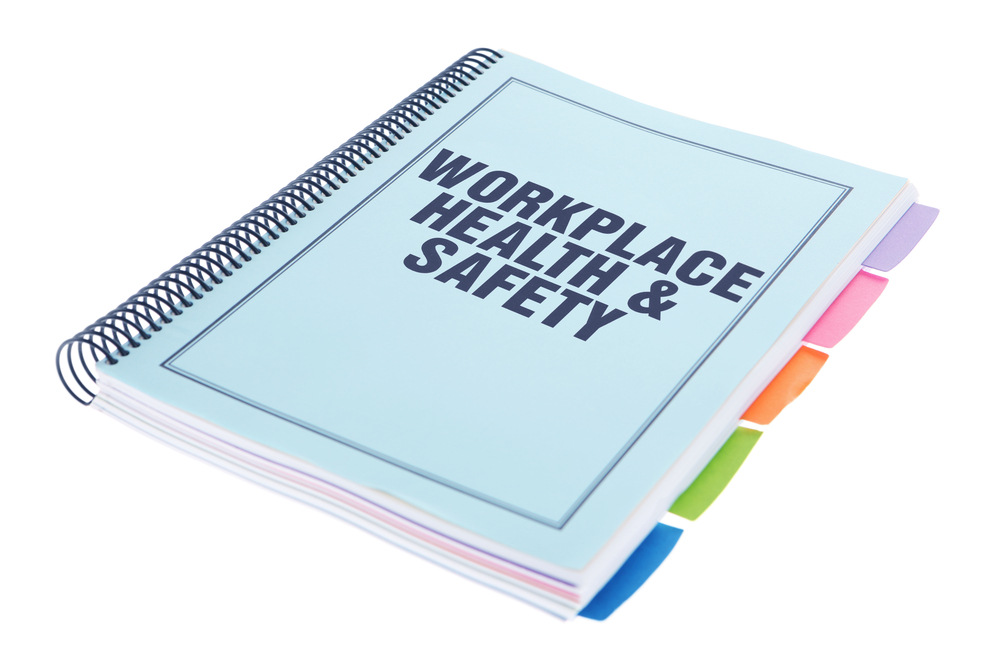
Improving health and safety standards in any organization can have a really positive effect on your business. Not only will your employees be safer, but it’s likely their job satisfaction and productivity will also increase, if meaningful improvements have been made. Robust health and safety practices can also be directly linked to a business’s bottom line, through the many fringe benefits it offers, such as improved procedures that make operations more efficient to reducing fines and unnecessary litigation that may arise when regulations are breached.
Have a clear health and safety policy
While a piece of paper with a system written on won’t change much and won’t protect anyone itself, what this does do is make sure that you have an understanding of your business, the risks that exist and the solutions that you can use. This is the first step which will underpin everything else you do when it comes to the health and safety of your workplace.
Assess
Assessing any potential risks by completing a health and safety risk assessment will feed into your health and safety policy. To do this, you need to look around your workplace and identify anything that has the potential to cause injury or illness. It might seem trivial. However, if there is a chance it can create risk then note it down and assess how likely the risk is to cause an injury and the possible extent of that injury. For many businesses, a risk assessment is a legal requirement, and insurance companies may demand to see one before they will consider offering a policy. It can also be used during an annual or other health and safety checks, to report on progress and identify ongoing areas for change. Going through your workplace and looking at what you do and how you do it and what could be done better allows you to understand what needs improving, what the real risks actually are and also will enable you to know how people work in reality.
Highlight
Not all changes can be implemented immediately, and in many cases, changes may not rectify the situation. Make sure that you have highlighted all the hazards and risk – this can include underlining potential dangers in health and safety policies, as well as underscoring hazardous areas using appropriate signage and other techniques. For example, low ceilings or raised floors can pose a hazard, but adding hazard signs will help prevent people from falling victim to them.
Improve
Once you have identified risks, you can then use these risk assessments to deliver improvement to your workplace. The more your staff see that you are making an effort, the more they will buy into a culture of health and safety. Make sure that they understand that health and safety is about physical improvements in the workplace, better guarding, more space – but it’s also about understanding where supervision needs to be better and understanding why staff may take short cuts. There are many ways to improve safety conditions, including through the provision of regular training and the offering of safety gear and equipment. Just knowing of potential hazards may not be enough to prevent employees from falling foul of those hazards. It is down to you, as the employer, to take suitable steps to mitigate the risk.
Also Read
Train
Training your employees will form the backbone of a lot of health and safety procedures and policies. Train staff on how to effectively set up their workstations to avoid Repetitive Strain Injuries, or have necessary training for those that work at heights. If you have judged a hazard to have minimal risk, it may not be required to offer training. Some job roles have mandatory training requirements anyway, and these are set out by law and are dependent on the role fulfilled by an employee, but also on jurisdiction. Make sure you’re up to date on the regulatory requirements as they differ from country to country, and can even vary from state to state and city to city. Training should also not be considered a one-off solution; you need to implement regular training updates to ensure that health and safety practices are at the forefront of your employees’ minds. This will also ensure that your team has access to the latest techniques and tips to help avoid injuries and illnesses.
Equip
Just training your employees isn’t always enough on its own and in some cases, you may need to provide safety equipment. Hazardous environments can mean something as simple as a noisy environment and required to offer your employees earplugs to help combat repetitive and loud noises. Then there is more obvious safety equipment such as harnesses to prevent falls from heights, high-visibility jackets and steel-cap shoes.
Maintain
Everything from safety equipment to the machinery and tools that employees use, need to be adequately maintained. Poorly maintained equipment can fail, and because your employees will expect the equipment to work, it may mean that they take fewer other precautions. As such, poorly maintained equipment can be worse than having no material at all. Make sure that you check all maintenance requirements for your machinery and arrange for regular checks. If any problems are reported with the mechanism, have them seen to quickly, because fixing a small problem is less expensive and safer than trying to remedy a colossal error.
Update
Just like the training, health and safety is not a one-off procedure that you can implement and leave it to run itself. Health and safety procedures and regulations need to be conducted regularly and routinely to ensure the continued safety of those on site. Policies should be updated with any new training requirements, safety procedures for new equipment and machinery, and with updated health and safety contacts within the working environment.
When you do update policies, make sure that employees are aware of the changes. Have them sign an update to the plan, and ensure that training is offered for any new updates.
Health and safety is a highly scrutinized area of business. Many people see it as unnecessarily complicated bureaucracy but, in reality, it saves lives and money, and it can prevent injuries and illnesses, so all employees should be encouraged to get on board with training and other processes. The law says that employers need to communicate, cooperate and co-ordinate – and they’re all valid points – but listen to your staff, watch how they work and understand why they work the way they do. It’s essential to talk about health and safety to your team as it’s all too common for health and safety to be mentioned once a month at the end of a staff meeting whereas sales targets are specified daily. I’m sure we have all heard someone say “hurry up – but take care” or something of that nature, so you need to make sure that your message needs to be clear and unambiguous – don’t mix the message or give the impression of lip service; they can quickly eliminate the positive things you say.
Manage and Supervise
Very often managing safety is forgotten and is not treated the same as the way we manage other aspects of the workplace. Don’t ignore lousy practice; make sure people are wearing their PPE where required. Staff do respond when we lead them effectively. Make sure that you, your management team and supervisors take ownership of their areas of responsibility, check on health and safety and make sure that safety inspections are done effectively. If you need to get professionals in to set a standard, then so be it, Texas Fire & Safety can schedule a free fire extinguisher walk-through of your company.
When conducting the safety inspections – investigate anything that you see that keeps cropping up. Clearing a blocked fire exit every week is better than leaving it blocked, but understanding why it’s getting blocked in the first place and providing a solution is the best option. This shows visible effort on your part, and that message reinforces everything that’s gone before.
There are no simple solutions to health and safety, signs are often used as a way of improving health and safety – and the odd one may help, most simply warn of residual risk – but if you implement a sudden flurry of posters then this is often viewed by staff as window dressing. Make sure that every step you take is a definite and aim to deliver real change. One of the most important things you can do though is to keep encouraging staff to report problems, accidents and even solutions.
Further reading about Health and Safety:
– Basic components of a safety audit
– Deciding when you need to call in a workplace accident lawyer.
– How to get qualified in health and safety