The modern supply chain is increasingly complex and globalized — and more often, it prioritizes maximum efficiency at the cost of slack and resiliency. While this makes it more profitable and less wasteful, it can also make it particularly vulnerable to major disruptions, like a hurricane, flood, trade war or viral outbreak.
While these disruptions and shortages are a fact of life, they can easily be devastating to businesses that are caught off-guard. Fortunately, any company can prepare for emergencies and stay resilient despite major disruptions to the supply chain, local infrastructure or the workforce.
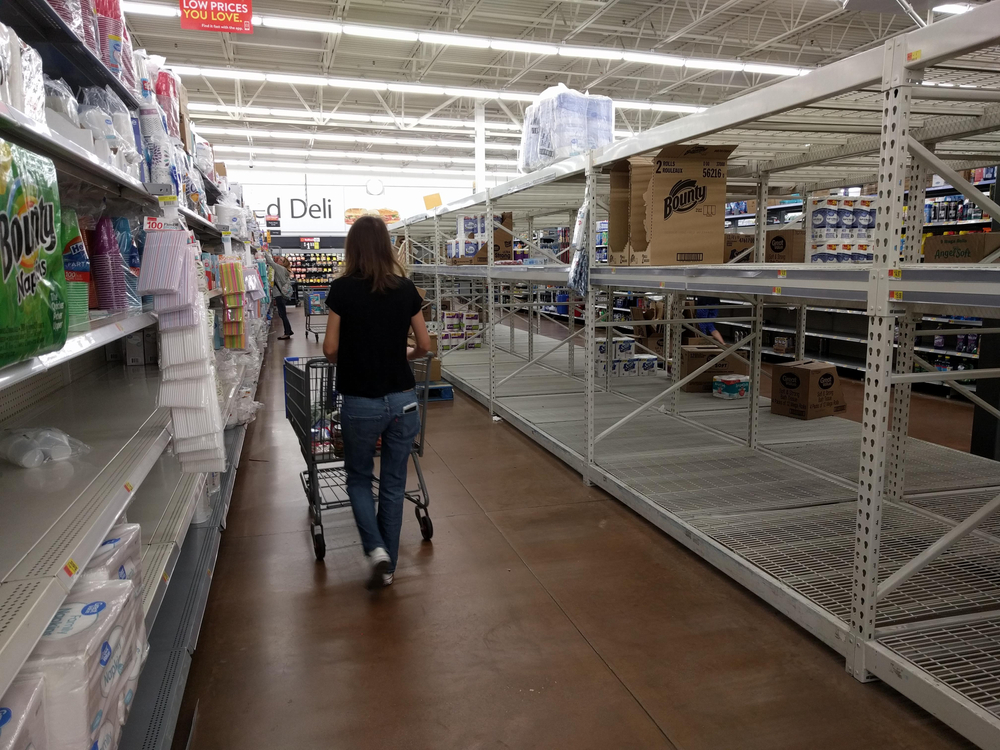
Shutterstock Licensed Photo – By Hayden Stirling
Here is how any business can develop a contingency plan to help them prepare for supply chain shortages and other disruptions.
Identifying Risks and Essential Resources
A good contingency plan helps identify potential crises, the impact they’ll have and how your business can respond to avoid the most severe consequences.
These plans typically identify vulnerabilities in your industry’s supply chain and plan for how your company can respond. Start with a supply chain vulnerability audit and a supply chain risk-management plan, if your organization does not already have one. There are many approaches to supply chain risk management, but being aware of and planning for the biggest dangers will be the most important.
Your business can’t predict every possible crisis, but it can identify potential disruptions — to infrastructure, supply chain and workforce — and plan how it will respond to each.
Also Read
Estimate how long your company will be able to keep running if you don’t have access to necessary supplies and raw materials. Investigate alternatives to current suppliers who may be vulnerable to a crisis. If you expect worker shortages, identify contractors who may be able to handle things your core team can’t fulfill.
Your business will need to be aware of which workers can’t be replaced, and the equipment and resources that are essential. A data center provider, for example, may not be able to weather the downtime and supply chain disruptions that can occur as a result of natural disasters.
The company may need to keep certain staff members on-site to keep the essential infrastructure running and the network online. Others may be able to work from home — but only if the right solutions are in place, and the business is prepared to transition to managing remote employees. The company may also need things like generator fuel or back-up equipment that can be difficult to obtain during a crisis.
Identifying these essential team members and resources ahead of time will help your business plan for how to respond to an emergency.
Once your contingency plan is drafted, be sure to keep it regularly updated. Risks are likely to shift and change over time, and an out-of-date plan may not provide the best possible response to an emergency.
Responding to Crisis
Once you’ve identified key staff, equipment and potential risks, you’ll need to plan for how your business will respond and follow through if normal operations are disrupted.
During the crisis, strive for transparency in customer relations. Communicate how your company is impacted by the event and what steps you’re taking in response. Make it clear how you’re prioritizing customer satisfaction — even if the crisis makes it impossible to provide certain products or services you typically offer.
Be prepared to communicate how long you expect the crisis to last and how customers will be impacted. Stay honest — you may not have all the information, but you can keep customers in the loop as best you can.
Consider reading up on crisis communications and the best practices for reaching out to your customer base in times of uncertainty. Communicate in a way that shows leadership and reassures customers.
You’ll want transparency in internal communications, too. No one likes uncertainty. People will feel more confident continuing to work through disruptions and shortages if your business can outline the steps it’s taking to ensure worker safety and the company’s continued success.
Major changes may be necessary to keep the business functional. If your company needs to rapidly shift directions or reprioritize operations, communicate this with both management and workers. If you plan to shut down in-store purchases and beef up delivery options, you’ll want all affected departments to know ahead of time, so they can make the best possible decisions.
Transparent and well-documented emergency procedures will also help ensure smoothest possible crisis operations. You can’t plan for everything, but you can identify supplies or raw materials your business won’t have access to. Plan for how you can work without them and still keep business as usual.
Guiding a Business Through Supply Chain Disruptions
Major emergency events can easily put critical orders and supplies on hold, make infrastructure unusable and disrupt the workforce. Businesses that don’t take steps to prepare can be especially vulnerable to these disruptions.
Fortunately, with the right planning, a company can become a lot more resilient. Identifying potential supply chain risks and critical equipment can help businesses plan for how they’ll respond in a crisis.