A successful manufacturing company can be very profitable; however, it can be a tough industry to crack. Keeping quality high whilst keeping costs down can be a precarious balancing act and mistakes can be easy to make. To ensure that your manufacturing company thrives, here are a few common mistakes to avoid.
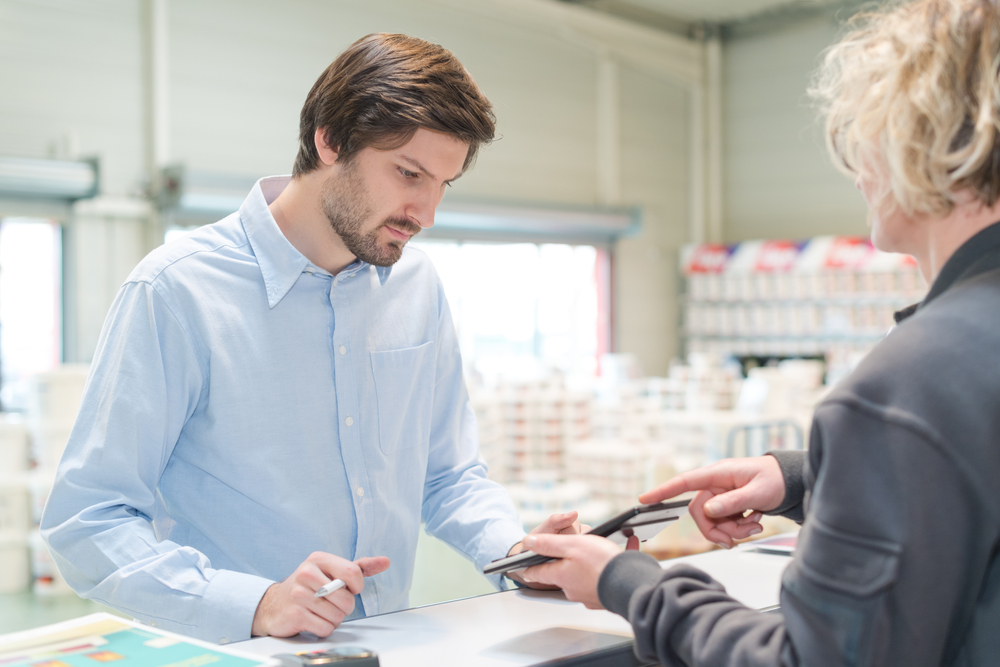
Shutterstock Licensed Photo – By ALPA PROD
Skimping on equipment
Your products will only be as good quality as the equipment you produce them with. Whilst not all cheap equipment is poor quality, a large percentage of it is likely to be not suitable for your needs. This could include old equipment that’s not in the best condition or budget equipment that may not be built for industrial use (such as a 3-D printer for personal use).
Mid-range equipment tends to be a better choice – although you should always rely on reviews. If you’re ordering custom-made machinery, check out reviews of the manufacturer. If you’re buying a pre-existing machine, look into reviews of the machine itself.
You don’t need to splash out on the most expensive equipment available. Some of the high-end stuff can be very specialist and you could be paying for a load of features you’ll never use. Unless you’re producing premium products, mid-range equipment is likely to provide the quality you need.
Refusing to adopt new tech
Technological advancements in the last 20 years have transformed the manufacturing industry. Smart sensors in machinery can now predict faults before they happen, whilst various processes can be automated. This helped to drastically improve productivity and lower costs.
Despite the clear advantages, some companies make the mistake of refusing to adopt this technology. This is usually because the hassle required to learn how to use and implement it, especially if a company has been using the same practices for many decades. Change can be tricky and scary, but it can be necessary for keeping up with competition and meeting the ever-increasing demands of customers.
Also Read
Of course, that isn’t to say that you should jump on every new tech trend. Not all new tech will help your business – it could be worth getting advice from a tech consultancy firm to help identify the right type of technology worth adopting.
Slacking on maintenance
Failing to maintain equipment properly can have all kinds of terrible effects. Certain equipment could be a health and safety danger if not fixed, whilst in other cases quality may be affected leading to products that aren’t up to spec.
Equipment should be regularly serviced by employees to check for faults (or you can use machinery with smart sensors as discussed earlier). Once these faults are identified, action should be taken quickly to repair or replace the machinery. A lot of businesses can delay repairs, which can cause faults to get worse – make sure to prioritize repairs (you may be able to get repairs done out of usual business hours if you don’t want to interrupt day-to-day business).
As well as servicing and repairs, it’s important to regularly clean equipment. Cleaning equipment can often help to prevent damage from dirt and dust, as well as helping to create a good visual impression for visitors. Some modern equipment is capable is cleaning itself, but generally some manual cleaning is needed which should kept to a schedule.
Ignoring energy usage
Manufacturing companies often have to deal with high energy bills due to the amount of electricity required to operate the various machinery. However, as many modern manufacturing companies have realized, there are various ways in which this energy usage can be cut down without affecting quality of manufacture. Cutting down energy usage could save your company huge costs. Not only that, but it could be beneficial for the reputation of your company by helping to lower your company’s carbon footprint.
There are a number of ways in which you can lower your company’s energy usage. This includes investing in energy-efficient equipment, shutting down machinery when not in use and possibly even installing solar panels to generate one’s own electricity. It’s possible to arrange an energy audit with the help of a business energy advisor to help cut down energy usage.
Rushing employee training
It’s also important to give your employees thorough training. Rushing employees through training can lead to mistakes as a result of human error. Some of these mistakes could be expensive to repair, whilst others could be a health risk.
The best manufacturers invest time and money into training staff so that mistakes are minimized. On top of training, it’s worth using signage and supplying handbooks to help guide employees. It’s worth noting that any changes to the company could require training everyone again – don’t expect employees to operate brand new machinery and understand brand new processes without a briefing.
Being too niche
Being too specific about the type of products you produce and types of customers you take on could limit the amount of business you’re able to get. Branching out into other types of products could mean having to buy new equipment, do new research and provide new training to employees – but in the long run it could be a worthy investment.
You’ll know your business is too niche if you’re struggling to attract customers. Boredom can also be an important sign that you need to try producing other products – a change of product could make your and your team more enthusiastic by creating a new challenge.
Diversifying doesn’t have to involve taking giant leaps. If you produce plastic piping, branching out into other plastic products could be wiser than delving into metalwork.
Failing to outsource
Outsourcing can help to save costs and save time by paying other companies to do tasks for you. In modern manufacturing it’s become commonplace.
In fact, many modern manufacturing companies are part of an interconnected manufacturing web – when it comes to products that may involve electronic parts, molded plastic and metal parts, it’s sometimes easier to outsource individual manufacturing companies than try to do all these jobs yourself. Outsourced manufacturers can also be used to create custom equipment and handle specific aspects such as jig and fixture design. This can help to ensure that equipment is personalized to your needs.
Outsourcing can also be useful when it comes to admin tasks like accounting, marketing and HR. You can even outsource someone to manage your supply chain – in essence, outsourcing someone to take care of outsourcing. Obviously, it is possible to outsource too much and end up paying others to do things that you can happily do yourself.
Expecting too fast a return
When starting up, many manufacturing companies can take several months to a year to start making any return. Being patient is important – cutting corners just so that you can pay off debts more quickly could negatively affect your reputation when it comes to quality. You do need to be making enough money for you and your employees to live on and if you’re running on a loss and building up debts, it could be worth talking to a financial advisor to find out what you can do to recover.